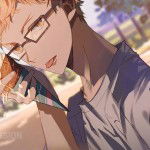
Introduction to Non-Ferrous Metals
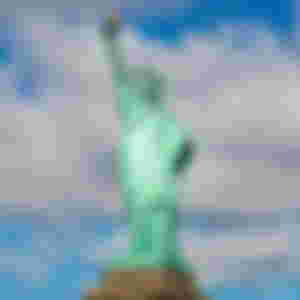
Statue of Liberty on Liberty Island in New York City, USA
We are surrounded by materials that undeniably amazing. In our kitchen, we see cooking tools, utensils and some sort of glasses, in our bedroom we see lampshades in the study table and a computer beside it, and to other places of the house, we see many materials that we are wondering about. No doubt that all the material things that we are having like phones, laptops, and other electronic devices came from a source that we really don’t care because it doesn’t highlight the material used upon purchasing like metal or something but only the main purpose of it to us human perhaps. Nevertheless, all the things that we see, we smell or even touch undergoes processes just like the gold jewelry that mesmerizes people, underwent from ore extraction. For instance, one of the famous statue known as “Statue of Liberty” on Liberty Island in New York City, USA, is the heaviest statue which comprises 31 tons (28.1 tonnes) of copper, 125 tons (113.4 tonnes) of steel, and 27,000 tons (24,494 tonnes) of concrete in the pedestal.
Basically, all the materials surrounding us are quite important. Little did we know that the phone that we are using, scrolling, playing, browsing or even discovering right now has material like metal in order to function. This certain thing is salient to effectively and efficiently use by the consumer. According to an article written by Bianca Nogrady, smartphones are pocket-sized vaults of precious metals and rare earth. A typical iPhone is estimated to house around 0.034g of gold, 0.34g of silver, 0.015g of palladium and less than one-thousandth of a gram of platinum. It also contains the less valuable but still significant aluminum (25g) and copper (around 15g).
Mostly, metals are broadly classified as ferrous and nonferrous. And those that are iron-free are used in some important gadget to prevent from corrosion. And these are called non-ferrous metals. Historically, nonferrous metals, especially the red metals, brought us out of the Stone Age and into the Copper and Bronze Ages. From 4500 BC to 1500 BC, copper and bronze dominated our primitive manufacturing systems. It wasn’t until 1500 BC that iron finally took hold as the most popular alternative for tools, weapons, and armor. Nevertheless, copper and bronze remained a staple in designer trades, like jewelry, interiors - and architecture. These metals invoke history, ancestry, and a throwback to nature. There is no other material on Earth that feels quite like a red metal. Nonferrous metals, including aluminum, nickel, lead, tin, brass, silver, and zinc, are known for their tensile strength and present characteristics that hold an advantage over ferrous metals, mainly by their malleability, lighter weight, and corrosion resistivity. As iron content is absent in nonferrous metals, the probability of rust and corrosion occurring also is fairly low yet the only difference lies in accessibility of these materials, recycling efficiency, and costs.
According to the study entitled Reliability and Maintainability of In-Service Pipelines, recycling of nonferrous metals, including aluminum, copper, brass, and lead, is relatively common due to its scarcity. Therefore, there is a heavy dependence on the recycling of scrap materials in order to create new nonferrous metals. In fact, aluminum is known to be the most recycled metal, ranking third in the world. It is also this reason that the cost of nonferrous metals is also more expensive than ferrous metals, with stainless steel often being used instead, due to its cheaper cost and versatility. (Mahmoodian, 2018)
Furthermore, nonferrous materials can be combined to create alloys, including brass, bronze, and solder, for increased strength and flexibility without resulting in the effects of heavier weight compared with ferrous metals. The high malleable state of nonferrous metals makes them ideal for usage as they can be easily pressed into thin sheets without breaking.
Overview of Metal Classification
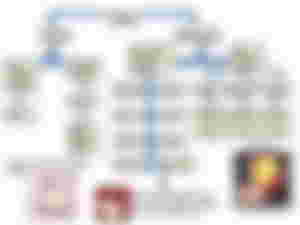
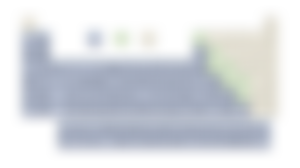
What Is Non-Ferrous Metals And Alloy?
Non-ferrous metals are those which do not contain significant quantity of iron or iron as base metal. This means that non-ferrous metals are not attracted to a magnet and they also do not rust in the same way when exposed to moisture. These metals possess low strength at high temperatures, generally suffer from hot shortness and have more shrinkage than ferrous metals.
They are utilized in industry due to following properties:
1. High corrosion resistance
2. Easy to fabricate, i.e., machining, casting, welding, forging and rolling
3. Possess very good thermal and electrical conductivity
4. Attractive colour and low density The various non-metals used in industry are: copper, aluminium, tin, lead, zinc, and nickel, etc., and their alloys.
Alloys are base metals combined with other metals or chemicals to enhance the base metals properties.
Non Ferrous Metals
Aluminium
It tends to be light in colour although it can be polished to a mirror like appearance. It is very light in weight.
Metal Uses
Used for saucepans, cooking foil, window frames, ladders, expensive bicycles.
Melting Point
660°C
COPPER and COPPER ALLOYS
Copper
It is a ductile and malleable metal. It is often red / brown in colour. It is a very good conductor of heat and electricity.
Metal Uses
Used for plumbing, electric components, cookware and roof coverings.
Melting Point
1084°C
MAGNESIUM AND MAGNESIUM ALLOYS
Magnesium
Magnesium is a fairly strong, silverywhite, light-weight metal (one third lighter than aluminum) that slightly tarnishes when exposed to air. In a powder, this metal heats and ignites when exposed to moisture and burns with a white flame.
Metal Uses
Magnesium is used in pyrotechnic (i.e. fireworks). It is alloyed with other metals to make them lighter and more easily welded.
Melting Point
648°C
Low Melting Alloys
ZINC
A bluish-white lustrous metal. It is very resistant to corrosion from moisture. However zinc is a very weak metal and is used mainly for coating steel.
Metal Uses
Used as a coating on screws, steel buckets etc. It is also used to galvanize steel.
Melting Point
419°C
TIN
It is a very ductile and very malleable metal. It is resistant to corrosion from moisture. It is bright silver in appearance. Tinplate is steel with a tin coating.
Metal Uses
Used as a coating on food cans, beer cans. Used as whistles, tin foil and soldering.
Melting Point
231°C
LEAD
It is a soft, malleable metal. It is also counted as one of the heavy metals. Lead has a bluish-white color after being freshly cut, but it soon tarnishes to a dull grayish color when exposed to air.
Metal Uses
Used for roof flashing. Also used for batteries and for X-ray protection.
Lead is used for its weight in many ways.
Melting Point
327°C
Precious Metals
SILVER
A soft, white, lustrous transition metal, it has the highest electrical conductivity of any element and the highest thermal conductivity of any metal. The metal occurs naturally in its pure, free form.
Metal Uses
Used for jewelry and high quality cutlery. Also used for currency coins and sports trophies. Used in mirrors as a reflective metal. Also, tableware, coinage, electroplating, photographic film etc.
Melting Point
961°C
GOLD
Gold is a dense, soft, shiny, malleable and ductile metal. Pure gold has a bright yellow color and luster traditionally considered attractive, which it maintains without oxidizing in air or water. Gold resists attacks by individual acids It won't tarnish, discolor, crumble, or be affected by most solvents.
Metal Uses
Used mainly for jewelry. Also used in co
mputers as a conductor. Used for its reflective powers to protect satellites. Coinage, dental work, electroplating etc.
Melting Point
1337°C
PLATINUM
Is a soft, ductile, grayish-white metal that has good corrosion resistance even at elevated temperatures.
Metal Uses
Used as electrical contacts, for spark plugs, as catalyst for automobile pollution-control devices, in filaments, in nozzles,as jewelry, in dental work, and in dies for extruding glass fiber.
Melting Point
1,768 °C
Non-ferrous metal alloys are metals that are a mixture of two or more metals. The main ones in everyday use are Brass, Bronze, Solder.
BRASS
Brass is a mixture of copper and zinc. Copper is the main component, and brass is usually classified as a copper alloy. The color of brass varies from a dark reddish brown to a light silvery yellow. Brass is stronger and harder than copper, but not as strong or hard as steel. It is easy to form into various shapes, a good conductor of heat, and generally resistant to corrosion from salt water.
Metal Uses
Brass is used to make water fittings, screws, radiators, musical instruments, and cartridge casings for firearms.
Melting Point
940°C
BRONZE
Bronze is a metal alloy consisting primarily of copper, usually with tin as the main additive. It is a hard and brittle metal. It has a very high resistance to corrosion.
Metal Uses
Used for ship propellers and underwater fittings. Also used for statues and medals.
Melting Point
950°C
SOLDER
Solder is a fusible metal alloy used to join together metal work pieces and having a melting point below that of the work pieces. It is an alloy of Lead and Tin.
Metal Uses
Solder is used for electronics, plumbing, jewelry making and repair processes where metal parts cannot be effectively or safely welded.
Melting Point
200°C
MORE NONFERROUS METALS
Mercury can be used to make thermometers, barometers and other scientific instruments. Mercury conducts electricity and is used to make silent, position dependent switches. Mercury vapor is used in streetlights, fluorescent lamps and advertising signs.
Tungsten is a rare metal and the free element is remarkable for its robustness. Highest melting point of all the elements and extremely hard material. It can be used as cutting blades, abrasives, armour piercing round Melting point 2870°C
Beryllium has 6 times the specific stiffness of steel. It is used to make rocket nozzles, space and missile structures, and aircraft disc brakes.
Zirconium is a flammable metal and is not found as metallic. It is silvery in color and is used in electronic components and in nuclear- power reactor application because of its low neutron absorption.
Cobalt is a bluish-white, lustrous, hard, brittle metal. It is ferromagnetic. Cobalt is used in alloys for aircraft engine parts and in alloys with corrosion/wear resistant uses, in batteries and in electroplating.
Cerium is a component of mischmetal, used in the manufacture of alloys for cigarette lighters. Cerium oxide is used in incandescent gas mantles, as a glass polishing agent and as a catalyst in self-cleaning ovens.
Cadmium's major use is in batteries (especially rechargeable nickel–cadmium, NiCad, batteries). Cadmium is used in low melting alloys and is a component of many kinds of solder.
Bismuth is a crystalline, brittle, metal and is used in medicine (bismuth subnitrate and subcarbonate), cosmetics (bismuth oxychloride), low-melting alloys, fire detection/extinguishing systems.
Indium is used to dope germanium to make transistors. It is also used to make other electrical components such as rectifiers, thermistors and photoconductors.
Niobium alloys are strong and are often used in pipeline construction. The metal is used in superalloys for jet engines and heat resistant equipment.
Gallium alloys are used in some medical thermometers as non-toxic substitutes for mercury.
Germanium is used in transistors and in integrated circuits. It is used as an alloying agent and as a catalyst. It is also used in infrared spectroscopes and infrared detectors.
Lithium is used in the manufacture of aircraft and in certain batteries. It's also used in mental health: Lithium carbonate is a common treatment of bipolar disorder, helping to stabilize wild mood swings caused by the illness.
Selenium is used in the glass industry to decolorize glass and to make red-colored glasses and enamels.
Tantalum is used in the electronics industry for capacitors and high power resistors. The metal is used in dental and surgical instruments and implants, as it causes no immune response
FAMOUS BUILDINGS MADE OF ALUMINUM
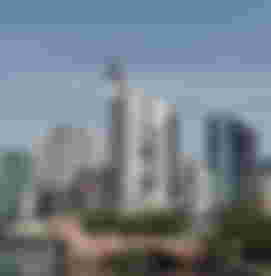
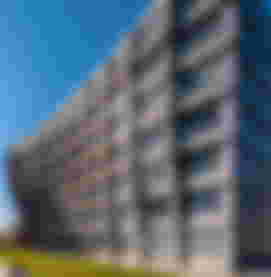
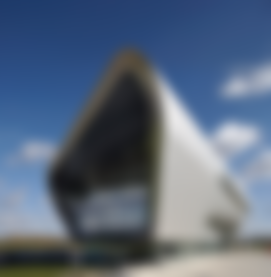
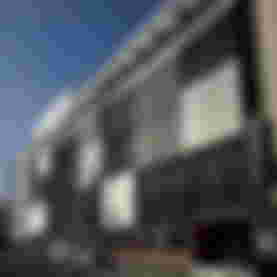
MATERIALS PROCESSING AND MANUFACTURING
The cycle of manufacturing processes that converts materials into parts and products starts immediately after the raw materials are either extracted from minerals or produced from basic chemicals or natural substances. Metallic raw materials are usually produced in two steps. First, the crude ore is processed to increase the concentration of the desired metal; this is called beneficiation. Typical beneficiation processes include crushing, roasting, magnetic separation, flotation, and leaching. Second, additional processes such as smelting and alloying are used to produce the metal that is to be fabricated into parts that are eventually assembled into a product.
The processes used to convert raw materials into finished products perform one or both of two major functions: first, they form the material into the desired shape; second, they alter or improve the properties of the material.
Forming and shaping processes may be classified into two broad types—those performed on the material in a liquid state and those performed on the material in a solid or plastic condition. The processing of materials in liquid form is commonly known as casting when it involves metals, glass, and ceramics; it is called molding when applied to plastics and some other nonmetallic materials. Most casting and molding processes involve four major steps: (1) making an accurate pattern of the part, (2) making a mold from the pattern, (3) introducing the liquid into the mold, and (4) removing the hardened part from the mold. A finishing operation is sometimes needed.
Materials in their solid state are formed into desired shapes by the application of a force or pressure. The material to be processed can be in a relatively hard and stable condition and in such forms as bar, sheet, pellet, or powder, or it can be in a soft, plastic, or puttylike form. Solid materials can be shaped either hot or cold. Processing of metals in the solid state can be divided into two major stages: first, the raw material in the form of large ingots or billets is hot-worked, usually by rolling, forging, or extrusion, into smaller shapes and sizes; second, these shapes are processed into final parts and products by one or more smaller scale hot or cold forming processes.
After the material is formed, it is usually further altered. In materials processing, a “removal” process is one that eliminates portions of a piece or body of material to achieve a desired shape. Although removal processes are applied to most types of materials, they are most widely used on metallic materials. Material can be removed from a workpiece by either mechanical or nonmechanical means.
There are a number of metal-cutting processes. In almost all of them, machining involves the forcing of a cutting tool against the material to be shaped. The tool, which is harder than the material to be cut, removes the unwanted material in the form of chips. Thus, the elements of machining are a cutting device, a means for holding and positioning the workpiece, and usually a lubricant (or cutting oil). There are four basic noncutting removal processes: (1) in chemical milling the metal is removed by the etching reaction of chemical solutions on the metal; although usually applied to metals, it can also be used on plastics and glass, (2) electrochemical machining uses the principle of metal plating in reverse, as the workpiece, instead of being built up by the plating process, is eaten away in a controlled manner by the action of the electrical current, (3) electrodischarge machining and grinding erodes or cuts the metal by high-energy sparks or electrical discharges, (4) laser machining cuts metallic or refractory materials with an intense beam of light from a laser.
Another further alteration may be “joining,” the process of permanently, sometimes only temporarily, bonding or attaching materials to each other. The term as used here includes welding, brazing, soldering, and adhesive and chemical bonding. In most joining processes, a bond between two pieces of material is produced by application of one or a combination of three kinds of energy: thermal, chemical, or mechanical. A bonding or filler material, the same as or different from the materials being joined, may or may not be used.
The properties of materials can be further altered by hot or cold treatments, by mechanical operations, and by exposure to some forms of radiation. The property modification is usually brought about by a change in the microscopic structure of the material. Both heat-treating, involving temperatures above room temperature, and cold-treating, involving temperatures below room temperature, are included in this category. Thermal treatment is a process in which the temperature of the material is raised or lowered to alter the properties of the original material. Most thermal-treating processes are based on time-temperature cycles that include three steps: heating, holding at temperature, and cooling. Although some thermal treatments are applicable to most families of materials, they are most widely used on metals.
Finally, “finishing” processes may be employed to modify the surfaces of materials in order to protect the material against deterioration by corrosion, oxidation, mechanical wear, or deformation; to provide special surface characteristics such as reflectivity, electrical conductivity or insulation, or bearing properties; or to give the material special decorative effects. There are two broad groups of finishing processes, those in which a coating, usually of a different material, is applied to the surface and those in which the surface of the material is changed by chemical action, heat, or mechanical force. The first group includes metallic coating, such as electroplating; organic finishing, such as painting; and porcelain enameling.
METAL RECYCLING
1. Collection
This is the first and most important step in metal recycling. It simply involves collecting all materials that are made of metals. This process should be organized in such a way that there should be containers specifically designed to collect metals. Some people and business persons have established scrap yards whereby people are encouraged to collect different metals, take them there and be paid for what they have collected. Different metals cost differently at the yards. The scrap metal yards are used as collecting centres for the metals.
2. Sorting
Once the metals have been collected, the next important step is to sort the metals. This involves separating what can be recycled form what is non-recyclable. It is essential to point out that the quality of metal recycled is very important. A high quality recycled product or item can only be created if the original materials used in the recycling process are of good quality. This therefore, calls for strict quality checkup during the sorting process.
3. Processing
After sorting, the next step is to compact or squeeze the metal. All the recycle materials are squeezed and squashed using machines so that they do not occupy so much space in the conveyor belts.
4. Shredding
After the crushing and breaking of the metal, the shredding process starts. The metals are broken down into tiny pieces or sheets to allow further processing. The small pieces have large surface to volume ratio that can be melted using less energy as compared to when they are in large pieces of metal. Normally, steel is changed into steel blocks while on the other hand aluminum is converted into sheets.
5. Melting and Purification
Melting of the scrap metal takes place in a large furnace. Each metal is taken to a furnace that is specifically designed to melt that particular metal based on its specific properties. The melting process uses a considerable amount of energy. However, the energy required for melting recycled metal is less compared to energy required to make metal from its raw material. The furnace is heated to appropriate degrees capable of melting the particular metal. Melting can take minutes or hours depending on how big the furnace is, the volume of metal placed in the furnace and the heat degree of the furnace.
6. Purification
After the melting process is complete, the next step is the purification process. Metals are purified using different methods. Purification of metals is done to ensure that the final product is free of impurities and that it is of high quality. Electrolysis is one of the methods of purifying some metals. Other metals are simply passed under powerful magnetic systems that separate metals from other recyclables. Today there are different purification methods depending on the type of metal.
7. Melting and Solidifying of the Metal
After the purification process, the molten metal is then carried by the conveyor belt to a cooling chamber where it is cooled and solidified. It is at this stage that the scrap metal is made into a solid metal that can be used again. Other chemicals are then added into the molten metal to make it acquire its density and other properties. It is at the cooling stage that different shapes and sizes of metals are made and designed.
8. Transportation of the Metal Bars
Once the bars have been designed and made, the final product is then packed depending on their sizes and shapes ready for transportation to different factories and to people who require the metal. Thereafter, the cycle begins again.
REFERENCES:
• Kalpakjian, Serope, and Schmid, Steven R. Manufacturing Engineering and Technology. Prentice-Hall, Fifth Edition.
• Lindbeck, John R. Product Design and Manufacturing. Retrieved from
https://www.fedsteel.com/our-blog/the-differences-between-ferrous-and-non-ferrous-metals-2/
· Tomwheats (2012)Ferrous and Non- Ferrous Metals . Retrieved from
https://www.slideshare.net/tomwheats/ferrous-and-nonferrous metals?next_slideshow=1
· Knapman (2012), Five Famous Aluminium Buildings Around The World. Retrieved from:
• Yukitaka Murakami, in Metal Fatigue (Second Edition), (2019). Retrieved from:
https://l.facebook.com/l.php?u=https%3A%2F%2Fwww.sciencedirect.com%2Ftopics%2Fengineering%2Fnon-ferrous metal%3Ffbclid%3DIwAR3oKw88oA_3H_pao1OWmrj1dLun7yj1dml
• Warner (2016). Thermal processing of metals. Retrieved from:
https://slideplayer.com/slide/6386024/
• Jackson, Hersman, Rinkesh (2020). Retrieved from:
https://www.conserve-energy-future.com/recyclingmetal.php
To all students out there that are having online classes and making endless paperwork and activities, welcome to the learner's community!
Here, you are free to share your outputs and turn it into an Article for others to learn from it as well.
Here's the link: https://read.cash/c/learners-community-b5b5
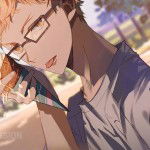
I like NY. Remember 11/09/2001 RIP