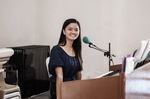
As an engineering student, we are into constructions of structures and buildings. Alongside with it, we are more engaged to the money that will be used and its cost estimation. Our professor gave us an activity where in, we are tasked to know more about Bill of Materials and the steps on how to make one.
Ps. No copyright infringement intended. For educational purposes only. References are given at the end of this article.
ABE 23: Activity 4
BILL OF MATERIALS
I. INTRODUCTION
A bill of materials (BOM) is a comprehensive list of parts, items, assemblies, subassemblies, intermediate assemblies, documents, drawings, and other materials required to create a product. The BOM can be thought of as the recipe used to create a finished product, presented in a hierarchical format. Depending on the product, it may include mechanical (hardware), electrical (e.g., ICs, PCBAs), software, and related documents and drawings.
An engineering bill of materials is also defined as the design of the finished product. It includes all alternative and substitute part numbers and parts contained in the drawing notes. Every line of the bill of materials (BOM) includes the product code, part name, part number, part revision, description, quantity, unit of measure, size, length, weight, and specifications or features of the product. The engineering BOM is often organized by engineers based on a computer-aided design (CAD) drawing. For a finished product, there may be more than one engineering BOM created. This is a part of product lifecycle management.
What is Included in the Bill of Materials?
The raw parts and labor itemized in the bill of materials are categorized based on the works involved in the construction process. Here are some of those items:
· Earth works. This involves all the labor used in processing parts of the land’s surface. It includes:
§ Excavation
§ Soil Poisoning
§ Backfill
· Concrete and masonry works. This involves all the labor and materials used in forming the skeleton frame of the house. It includes:
§ Cement
§ Sand
§ Gravel
· Steel and reinforcement works. This involves all the labor and materials used in strengthening the structure of the house. It includes:
§ Footings and columns
§ Beams
§ Slabs
· Architectural works. This involves all the labor and materials used in completing the architecture of the house. It includes:
§ Floor finishes
§ Wall finishes
§ Ceiling finishes
§ Doors
§ Windows
§ Tiling works
· Electrical works. This involves all the labor and materials used in installing power apparatus and equipment. It includes:
§ Roughing in
§ Wiring
§ Lighting
§ Panelboard mounting
· Plumbing works. This involves all the labor and materials used in installing the system of pipes and tanks required for water supply and sanitation. It includes:
§ Fixtures (faucet, shower valve, floor drain, shower drain, kitchen sink)
§ Drainage Line System (sewer line, water line, storm drainage)
· Painting works. This involves the labor and materials used in finishing the house.
II. RATIONALE
Importance of Bill of Materials
· A BOM list is necessary when building a product and ordering replacement parts and reduces possible issues if product repairs are required. It helps to plan for acquisition orders and reduces the possibility of errors.
· It tells how much exactly the construction is. With this, you’ll be able to make the financial preparations required to complete the project. Moreover, you know where your money will be spent.
· It allows you to check the quality of the build. Given that the items to be used will be itemized, you’ll have a rough idea of the strength, durability, or even the energy-efficiency of your walls, roofs, and ceilings. You can check whether the materials to be used match or did not match the build you’re envisioning for your home.
· It’s required by the local government. To get a building permit and start your construction, you must submit a copy of the bill of materials to your local government.
· By providing a single record of the materials, components and assemblies that go into the product, a bill of materials ensures these items are in-house when needed and at the quantities required during production. This minimizes inventory inaccuracies and production delays, both of which cost time and money.
· Bills of materials also ensure uniformity. When each production run follows the same BOM, the products themselves remain consistent. This helps ensure they meet customer expectations and is critical when products need to meet safety or other standards.
· The information contained within BOMs also is key when it becomes necessary to track product failures. With this document, it’s possible to identify the parts, materials and components used and zero in on potential sources of failures. Manually preparing and managing BOMs can quickly become unwieldy and error prone. Software, such as a supply chain and inventory management solution, can help automate the development process.
III. STEPS IN CREATING BILL OF MATERIALS
1. Answer the Critical Questions
Before creating a BOM for your next product, you should have the answers to the following questions:
· What’s being built?
The design is really what kicks off a BOM in most capacities. Depending on the complexity of the program or build, there will usually be multiple BOMs. These will create the finished assembly BOM. Start by compiling as much information as possible about the parts you need as the designs progress. Understanding what’s being built and/or the program design will be the key to creating a successful BOM.
· How will the BOM be managed?
As the BOM is created, it’ll likely go through multiple revisions and touch many different departments and people. Before creating the actual BOM, establish a system for managing it and ensure the latest version is used. Always track changes and create identifiers for the different versions. The less people allowed to interact with or edit the document, the better. It’s a good idea to decide ahead of time who’ll be responsible for what tasks to avoid confusion down the road.
· Who can access and use it?
Due to the range of information the document includes, it’s likely multiple departments – including but not limited to design, engineering, purchasing, and manufacturing – will use it at some point during the production process. Having an idea of who requires BOM access will help maintain that the correct information is included.
· What information should be included?
Although the specifics aren’t required at this point, you should have an idea of what categories the document will include. Every BOM should consist of some basics, such as part name and quantity, but other items are optional (we’ll cover these in another blog in the future). Regardless of the information determined to include in the BOM, keep in mind that it should be as detailed as possible.
· How should the BOM be organized?
It’s helpful to decide on basic organization strategies before you begin. Consider the following: number of levels and sub-assemblies; items assembled, separately, and then attached to the main assembly; and outside processing or other special designations. Ensure parent and child parts are aligned accordingly.
· What program will be used to create the BOM?
Before a BOM can be created, you need to decide which software application to use to maximize your team’s productivity. Excel is probably the most used, but not necessarily the most effective. As projects become more complex, there may be a need for more advanced spreadsheet-style and/or collaborative web-based applications specifically designed for BOMs, like Plan for Every Part (PFEP) software.
2. Create the Document
Open the program planned for use and create a new spreadsheet document. Name the file and put the name of the project and any other important identifying information in the title and at the top of the document. For example, “Company Name – Program Name – Assembly – Date”.
3. Organize the Document
Establish user permissions, set up change tracking, and create any levels required. Organization throughout the BOM process will be necessary as it’ll be an ongoing activity. Be consistent with organization.
4. Fill in the Columns
Populate the names of the categories at the top of the columns. These titles will include things such as part name, quantity, part number, etc.
5. Fill in the Rows
Populate the rows with information according to the category of the column. Each assembly, sub-assembly, part, process, etc. will have a separate row. Ensuring that information is accurate and up to date is critical to the success of the project.
6. Update as Needed
Update the information in your BOM as necessary. As the file is prepared, remember to save it often and keep a record of changes. As more information is learned on a given project or build, changes will be required. Flexibility is key throughout the production process.
IV. CONCLUSIONS
Bill of materials is like a cooking recipe. For example, you’re just a beginner in terms of cooking, then you’re trying to cook without recipe. Will you be able to cook successfully? The recipe provides the ingredients needed along with the quantities required. It also provides instructions on how to combine the ingredients as well as how to combine them and the cooking times and temperatures required. Without a recipe, the cake will almost certainly be a flop.
It therefore is obvious that a well thought out and detailed BOM is a vital part in the construction industry. Without it, the project is likely to be incorrectly costed and suffer major stock shortages and delays, to mention just two of the main problems. An accurate, complete BOM helps identify the cause of a product failure and work quickly to replace the faulty parts, materials, and components.
V. REFERENCES
Jenkins, A. (2021), “What is a Bill of Materials (BOM)? Expert Guide and Tips”, Oracle Netsuite, Retrieved from https://www.netsuite.com/portal/resource/articles/erp/bill-of-materials-bom.shtml
Kudla, C.H. (2019), “Bill of Materials in Construction”, Omni Accounts, Retrieved from https://www.omniaccounts.co.za/articles/bills-of-material-in-construction
Lamudi Philippines Inc. (2019), “Bill of Materials Sample: What You Need to Know”, Retrieved from https://www.lamudi.com.ph/journal/bill-materials-sample/
Lancione, T. (2019), “BOM 101: 6 Steps for Preparing a Successful Bill of Materials”, Industry Star, Retrieved from https://www.industrystar.com/blog/2019/04/6-steps-preparing-successful-bom/
PTC Inc. (2021), “What is an Engineering Bill of Materials (EBOM)?”, Arena: A PTC Business, Retrieved from https://www.arenasolutions.com/resources/articles/engineering-bom/
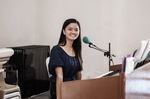