
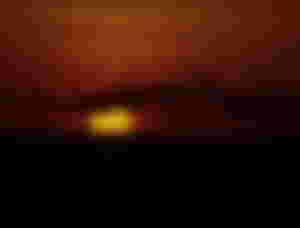
Sunday the issues still ok, not too many pop up. But still a few from them:
R&D UNDER ETCH
WET SINKER
3 rnd lots underetch (whole lot - whole wfr affected). Measured remaining thickness ~1200A highest. Diff flow from std productions. All 3 lots from BRC4 (all 3 lots batched) . temperature check on monitor at 32.2C, measured at 32.5C.
Incoming thickness for 1st ox at 14833-14843A. No splits on template. ER for 8A: 1450A/min. Time on runsheet is 9m20s, based on calculation etch time should be ~11mins
Took #25 from batch3 to re-etch 1min, inspected ue cleared. Rest of wfrs havent re-etch. Lots hold for device to verify etch time
RESIDUE STRIP WET RESIST
BACKGROUND:
Whole lot seen with rsd on s/l. Buddy run in B04,BL: 29 PL1 inspected no similar rsd seen. Rsd seen randomly across the wfr but edges affected more. Severity <3%.
Initially lot max delay aft oven. , Buddy run/lot bfr/aft in no issue. Buddy run/lot bfr/aft no issue.
PWB1 CONVERSION TO AZ300T
----------------------------------
Refer to YS's email. Pls help to cascade to operator about change. Already paste the conversion checklist on the bench. Chemical outside the grey area lift.
Conversion checklist pasted on tool. PM tech Sel feedback they will perform pm and conversion at the same time. Surfscan passed at 9p. Temp set to 82+/-3C
Release all metal etch/tre process. 1st run, inspected 10pcs under DF, seen with slight particles in die and photodiode. Photos saved. Expedite lots to supr and adv hold at every step to inspect. Tool up for prod.
