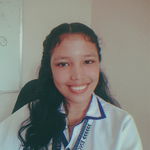
BRANCH CIRCUITS
· A branch circuit is defined as that part of an electric circuit extending beyond the last circuit breaker or fuse. The branch circuits start at the breaker box and extend to the electrical devices connected to the service. Branch circuits are the last part of the circuit supplying electrical devices. These circuits are classified in two different ways, according to the type of loads they serve or according to their current-carrying capacity.
TYPES OF BRANCH CIRCUITS
General Purpose Branch Circuit
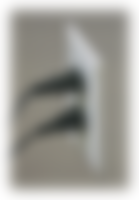
General purpose branch circuits are 120 volts circuits used for supplying lighting fixtures and receptacle outlets for most small portable appliances. There are usually a number of general purpose branch circuits supplying lights and outlets in different rooms around a residence or commercial or industrial building.
Circuits rated for a maximum of 15 amps using 14 gauge wire were common in older homes but are no longer recommended in new installations. Circuits rated for a maximum of 20 amps using 12 gauge wire are recommended for general purpose branch circuits in modern electrical wiring systems.
Appliance Branch Circuits
· Appliance branch circuits are 120 volts circuits used for supplying fixed electric equipment such as refrigerators, washers, and other large appliances and electrical devices. Appliance branch circuits do not supply any lighting fixtures. Appliance branch circuits can not exceed 20 amps.
Individual Branch Circuit
· Installed in permanent locations such as an electric range, a clothes dryer, or an air conditioner. These circuits usually lead directly from the distribution panel to the appliance and do not serve any other electrical devices. These circuits can be any amperage size.
General guidelines in planning the electrical system in the farm residence.
· National Electrical Code — The NEC establishes minimum standards required to assure safety and reduce risk of electrical system failure. Wiring materials and devices should bear the label of a recognized testing agency such as the Underwriters Laboratories (UL), Electrical Testing Laboratories (ETL) or Factory Mutual (FM)
· Electrician — Use of a licensed electrician is recommended. Licensed electricians are more likely to be familiar with requirements of the NEC and accepted good practices.
· Electrical Service — Each building should have only one electrical service. The service entrance panel must have a main service disconnect and should be surface mounted on a fire-resistant surface in a clean, dry room
· Grounding — All service entrances must be provided with a grounding electrode (ground rod, minimum 8 feet) and a properly sized (based on service capacity, NEC Table 250-94) grounding Figure 1. Use of UL listed equipment and installation in accordance with the National Electrical Code helps assure safety and a long service life. electrode conductor properly clamped to the electrode
· Wiring Location — Surface mount all wiring (cables and conduit) to facilitate maintenance and inspection, minimize rodent damage and reduce moisture migration. Under no circumstances should wiring be concealed within the walls or extended into the attic or ceiling spaces
· Conduit — Use nonmetallic conduit where multiple circuit conductors are needed or where wiring is subject to physical damage. Schedule 40 conduit is appropriate for general wiring.
· Branch Circuits — Use No. 12 AWG or larger copper wire for all 115 volt general purpose circuits. No. 14 AWG copper wire should only be used for circuits with known, controlled loads. Conductors servicing continuous loads (such as heat lamps and fans) must be larger
· Equipment Grounding — All equipment and all metallic components of the electrical system and building within 8 feet of the floor or soil surface must be bonded to the grounding electrode system (NEC 250-42). A grounding electrode (rod) at the site of a piece of metallic equipment is not permissible, except as a complement to a grounding conductor (bare copper or green insulation) from the service distribution panel.
· Switches and Receptacles — Equip all devices with dusttight and watertight corrosion-resistant, gasketed covers. When mounted on a vertical surface, hinge the cover at the top. Single pole switches installed with spring-loaded covers must be installed so they are "off" when in the down position.
Selection of the service-entrance switch
· knowledge is how critically important service entrance switchgear is as a link. If you have trouble with it, your whole building is out of power.
· it must be appreciated that not all service entrance switchgear is created equal. Some equipment is built to manufacturing standards that assume the best possible conditions, like a clean and dry indoor location, which is not realistic in many cases. You’ll have to deal with electrical rooms where there are sprinklers and where leaks and minor floods can occur. Equipment that’s tolerant for these conditions operates more reliably in the long run.
· You’ll also want to consider quality. Well-built service entrance switchgear incorporates certain design features, such as welded construction for outer enclosure, power fuses (as opposed to current-limiting fuses) and copper bus instead of aluminum bus. Service entrance switchgear that is built to lower quality standards will result in more frequent maintenance needs, whereas equipment built to higher quality standards will reduce the number of outages.
· Another factor to consider is customization, since every service entrance switchgear project comes with its own unique requirements. Retrofitting switchgear in an existing electrical room will experience certain design constraints, such as ceiling height. Standard designs typically occupy a larger space, particularly in terms of headroom, so a customized solution that is lower-profile may be required instead. Having to raise the ceiling in a room to accommodate your service entrance switchgear, after all, would result in immense costs or may otherwise be unfeasible.
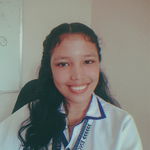