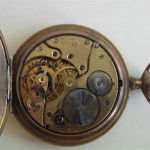
Silicon is a shiny, semiconducting metallic element used in the manufacture of steel, aluminum, solar photovoltaic cells, and of course, computer processor chips.
After oxygen, silicon is the most abundant element contained in the earth's crust, representing nearly 30% of its mass. However, as a simple body it is not found in pure form in nature. It is generally bound to oxygen in mineral form.
This type of silicon is found in abundance in the form of silicon dioxide (SiO2), quartzite, quartz, ordinary beach sand, and hundreds of other mineral compounds.
It was the Swedish chemist Jöns Jacob Berzelius who was the first to isolate and describe elemental silicon in 1824. However, the ability to isolate and mass manufacture high purity metallic silicon would not be achieved until much later. .
For almost five thousand years, humans have been transforming the silicon dioxide in sand into glass , constantly improving their ability to do so. The production of silicon-based glass transformed our collective ability to create art, glassware, and later to develop the optics that would help found the ideas of the Scientific Revolution, circa 1540 to 1650.
The use of glass in early scientific instruments revolutionized scientific understanding, contributing to major discoveries in physics, astronomy, chemistry, and biology. This revolution continued with the advent of improved glassblowing and the wider range of more sophisticated instruments it allowed.
The rise of the industrial revolution, the improvement in glass technology deployed in microscopes, telescopes, thermometers and an endless plethora of laboratory instruments, transformed our understanding of the natural world.
Glass continues to provide an invaluable service to the development of industrialized society, from the high-strength, scratch-resistant glass found in billions of cell phones and computer screens, to glass protection used for windows in our homes, offices and vehicles or more common glass used in a million other applications.
Humanity produces around 6.7 million tonnes of silicon per year. About 80% is produced as ferrosilicon used in the manufacture of iron and high performance steels with properties of resistance to high temperatures and corrosion, or used in alloying with aluminum. The alloy of aluminum with silicon improves its strength and corrosion resistance, while improving the metal casting performance; it is commonly used in casting and engine production.
A very small proportion of the high purity silicon dioxide extracted each year - around 15% - is destined to become the raw material for the wafers that are the central processing units of billions of cell phones and computer systems.
The first functional silicon transistor was developed in 1954 at Bell Labs by an American physico-chemist, Morris Tanenbaum. The transistor was rather badly received at the time, and few could have speculated with precision how silicon transistors were going to radically transform the progress and growth of society.
Processor-grade polycrystalline silicon (a highly purified form of metallic silicon) is the base material for the wafers on which central processing units are built.
However, it is common but wrong to think that the silicon in computer chips is made from sand from some beach. While it is true that silicon chips are made from sand, it is by no means ordinary sand.
Silicon dioxide in the form of sand fills our beaches, covers the bottom of deltas in rivers and oceans, and covers our deserts. However, not all of the sand in Saudi Arabia will provide civilization with the silicon needed by a single microprocessor. To achieve the surprisingly high levels of silicon purity required, the source material itself must be of unsurpassed purity.
These sources of ultra-pure silicon dioxide are mined in only a few places around the world, perhaps most notably at a cluster of small mines in Spruce Pine, Tennessee. The high purity white silicon dioxide open pit mines are so bright they glow like a beacon when viewed from Google Earth.
Once mined, the silicon dioxide source rock must be washed, crushed, filtered to remove impurities, conditioned and prepared for smelting. Pure elemental silicon must be freed from oxygen bonds by melting at a very high temperature in a powerful electric arc furnace.
Silicon dioxide is mixed with two main sources of carbon, usually charcoal and wood, and placed in the kiln, where the added carbon helps to remove oxygen in the form of carbon dioxide gas. 99% pure elemental silicon is thus obtained.
Unfortunately, from the point of view of the computer processor, a purity of 99% looks like a desert. What is needed is an ingot of 99.9999999999999% purity. This represents one atom of non-silicon for every seven billion atoms of silicon. This equates to one person out of the entire human population.
To achieve this astonishing level of purity, metallic silicon is subjected to a series of chemical processes. These processes convert metallic silicon into silicon tetrachloride - a compound necessary for the production of high performance fiber optic glass that carries 99% of the world's intercontinental communications data through some 285 submarine data cables.
The secondary product, trichlorosilane, is then transformed into polysilicon, the ultra-pure silicon that will be transformed into silicon computer wafers. From there, the polysilicon is melted at high temperature and under an inert gas atmosphere, in a pure quartz crucible.
The molten crucible is kept rotating and a seed crystal of ultra-pure silicon is inserted, on which the molten silicon in the crucible begins to grow. As it grows, the crystal is carefully pulled - up and out - from the melt in an extremely slow continuous motion. When finished, a single crystal of pure silicon was grown, with a mass of about 100 kg, or 220 pounds.
Ingots are precision cut and polished to achieve a flawless mirror finish. The most perfect of these circular discs of pure silicon are the support on which the architecture of the computer processors of modern central units is engraved. Other wafers are made into the base material for solar cells.
The quality, purity and physical properties of finished silicon wafers have not changed dramatically over the past decade. However, the architecture of microprocessors engraved on this silicon has improved a lot. Silicon is a perfect example of a material resource of little intrinsic value, until humans endowed it with the ability to do useful work.
Over the next decades, silicon will continue to form the basis of our digital age. Silicon is a testament to civilization's ability to transform a seemingly worthless mineral resource into one of the most technologically advanced and valuable products humanity has created.
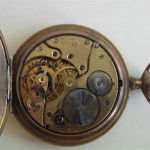